Ceramic Band Heaters, Knuckle Band Heaters-Construction
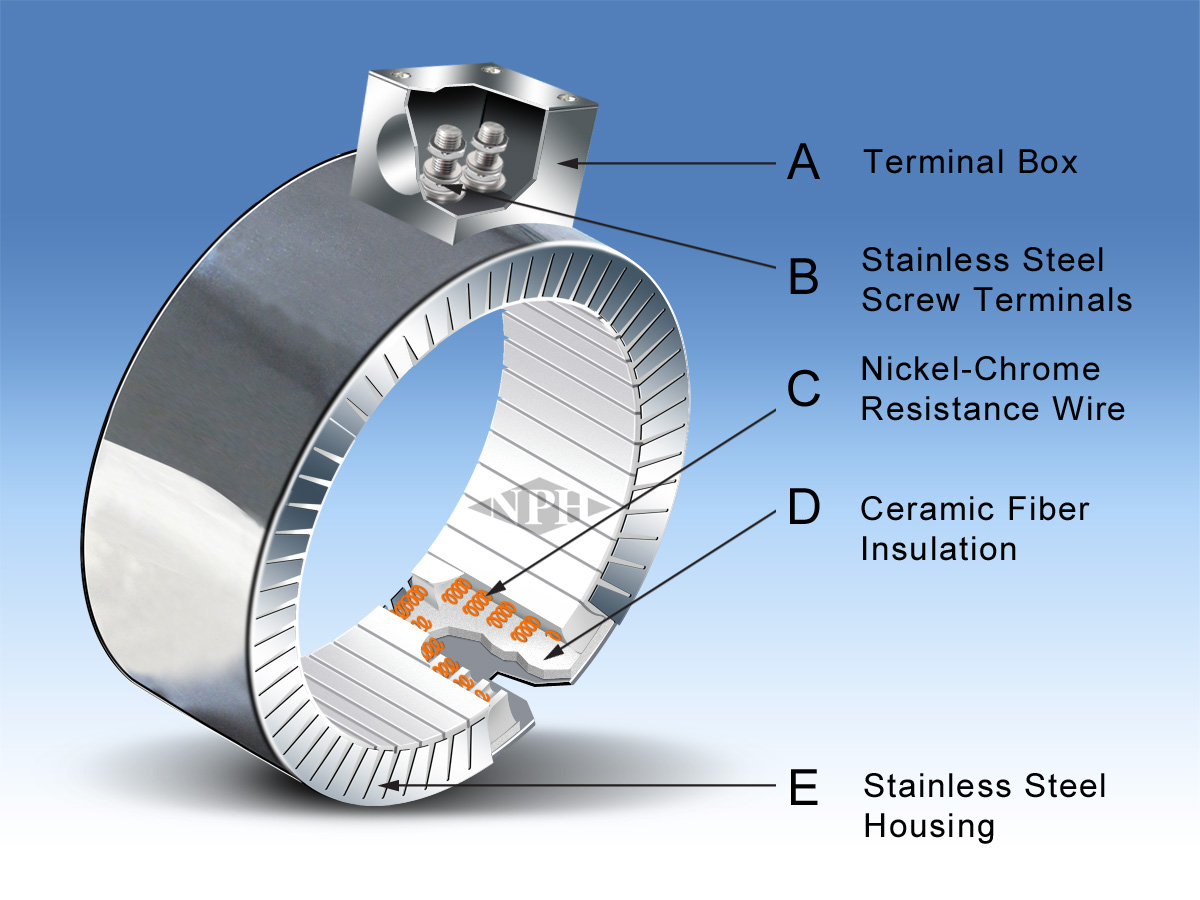
Ceramic Band Heaters, Knuckle Band Heaters-Construction
Construction Features- Ceramic Insulated Knuckle
Band Heaters
A. General purpose terminal box offers excellent protection to exposed
terminals. To simplify electrical wiring, the box has a ½" trade size knockout (actual dis.
7/8") that will accept standard conduit or flexible armor cable connectors.
B. Stainless steel screw terminals connected to solid nickel pins designed to provide maximum amperage carrying capacity.
C. Built-In ceramic fiber insulation ¼" thick standard on all Ceramic Bands will reduce power consumption by 25 to 30 percent. Further reduction can be obtained with optional ½" thick insulation. Specially designed mounting brackets with ¼"-20 socket cap screws are used to securely draw the heating element assembly against the cylinder evenly and tightly across its entire width. Brackets are located 180* from the screw terminals.
D. Helically wound nickel-chrome resistance wire strung through specially designed ceramic insulating bricks.
E. Stainless steel housing with serrated edges provides maximum flexibility for ease of installation.
Â
Ceramic Band Heaters, Knuckle Band Heaters ¢â‚¬â€œ Description
In a ceramic band heater, nickel-chrome wire is embedded in a flexible outer wall made of special, interlocking ceramic tiles, which are assembled like a brick wall. Ceramic fiber insulation and a stainless steel jacket or shroud cover this assembly. This construction prevents heat loss and reduces electrical consumption by 20% to 30%.
An energized ceramic band heater will have a temperature of 350 to 450 degrees F on its outside shell when the inside temperature is maintained at 1200 degrees F. To improve the conservation of energy, different thickness of ceramic fiber insulation mats are available.
Heat is transferred from a ceramic heater to the surface of an application through conduction and radiation. This is why a tight grip on the cylinder is not as critical as in other types of heaters. Moreover, over tightening should be avoided, since the pressure on the insulation mat reduces its insulating efficiency.
Ceramic band heaters are made by using different combinations of ceramic tiles, which are available only in specific lengths. Consequently, the width of a ceramic band heater band falls within a certain incremental range.
Ceramic band heaters can be manufactured with different clamping mechanisms, terminations styles, holes and cut-outs.
Ceramic band heaters are medium-to-high temperature heaters that have 1200‚ºF as a maximum working temperature. These durable heaters have in-built ceramic fibre jackets that make them energy efficient. Ceramic band heaters are available with different terminal styles, are fully flexible, and can accommodate holes and cut-outs.
Ceramic Band Heaters by NPH provide long life and use less wattage (because of insulation) in plastics extrusion and injection molding applications. These band heaters are constructed with a stainless steel shroud enclosing high quality ceramic knuckles through which run coiled high temperature nickel-chromium element wire. Configuration choices allow selection of one or two piece heaters, type of closure, and type of leads/post terminals. Diameters of 2-1/4" or greater and widths of 1" to 16" are available. Leads normally exit 180‚° from gap. Options include terminal boxes, holes, Heat Saver (extra) insulation, 3-phase power, dual voltages, partial coverages, European connectors, and perforated sheaths without insulation for air cooled applications. To order, specify quantity, configuration, inside diameter, width (increments of 1/2"), wattage, voltage, lead length if applicable and any options.
B. Stainless steel screw terminals connected to solid nickel pins designed to provide maximum amperage carrying capacity.
C. Built-In ceramic fiber insulation ¼" thick standard on all Ceramic Bands will reduce power consumption by 25 to 30 percent. Further reduction can be obtained with optional ½" thick insulation. Specially designed mounting brackets with ¼"-20 socket cap screws are used to securely draw the heating element assembly against the cylinder evenly and tightly across its entire width. Brackets are located 180* from the screw terminals.
D. Helically wound nickel-chrome resistance wire strung through specially designed ceramic insulating bricks.
E. Stainless steel housing with serrated edges provides maximum flexibility for ease of installation.
Â
Ceramic Band Heaters, Knuckle Band Heaters ¢â‚¬â€œ Description
In a ceramic band heater, nickel-chrome wire is embedded in a flexible outer wall made of special, interlocking ceramic tiles, which are assembled like a brick wall. Ceramic fiber insulation and a stainless steel jacket or shroud cover this assembly. This construction prevents heat loss and reduces electrical consumption by 20% to 30%.
An energized ceramic band heater will have a temperature of 350 to 450 degrees F on its outside shell when the inside temperature is maintained at 1200 degrees F. To improve the conservation of energy, different thickness of ceramic fiber insulation mats are available.
Heat is transferred from a ceramic heater to the surface of an application through conduction and radiation. This is why a tight grip on the cylinder is not as critical as in other types of heaters. Moreover, over tightening should be avoided, since the pressure on the insulation mat reduces its insulating efficiency.
Ceramic band heaters are made by using different combinations of ceramic tiles, which are available only in specific lengths. Consequently, the width of a ceramic band heater band falls within a certain incremental range.
Ceramic band heaters can be manufactured with different clamping mechanisms, terminations styles, holes and cut-outs.
Ceramic band heaters are medium-to-high temperature heaters that have 1200‚ºF as a maximum working temperature. These durable heaters have in-built ceramic fibre jackets that make them energy efficient. Ceramic band heaters are available with different terminal styles, are fully flexible, and can accommodate holes and cut-outs.
Ceramic Band Heaters by NPH provide long life and use less wattage (because of insulation) in plastics extrusion and injection molding applications. These band heaters are constructed with a stainless steel shroud enclosing high quality ceramic knuckles through which run coiled high temperature nickel-chromium element wire. Configuration choices allow selection of one or two piece heaters, type of closure, and type of leads/post terminals. Diameters of 2-1/4" or greater and widths of 1" to 16" are available. Leads normally exit 180‚° from gap. Options include terminal boxes, holes, Heat Saver (extra) insulation, 3-phase power, dual voltages, partial coverages, European connectors, and perforated sheaths without insulation for air cooled applications. To order, specify quantity, configuration, inside diameter, width (increments of 1/2"), wattage, voltage, lead length if applicable and any options.
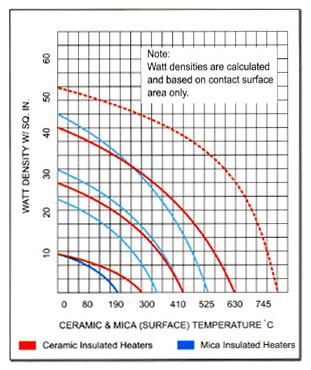
Ceramic Insulated and Mica Insulated Band Heaters-
Watt Density and Surface Temperature
Watt Density and Surface Temperature
Advantages of Ceramic Knuckle Band Heaters:







COMPARISON OF INSULATED VERSUS NON-INSULATED
BANDS IN TERMS OF WASTED
ENERGY
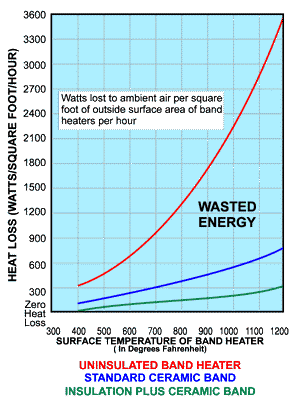
The Ceramic Insulated Knuckle Band Heater, May Be Divided
in 4 Main Parts:




Heating Coil - The helically wound heating coil is the actual resistance which is where the electrical load occurs. The most common type of metal alloy used for this purpose is a Nickel-Chromium mixture, also known as Nichrome. The Nichrome wire is wound around a ceramic core, and the number of spirals per inch vary according to the requested watt density. Potential from an alternating current source, which can either be 2 phase or 3 phase, flows through the coiled Nichrome wire, heating up the wire, which in turn, heats the cartridge heater sheath.
Insulation - Built in ceramic fiber insulation is used to prevent the Nichrome coil to contact the sheath. If such event happened, it would ground the resistance and produce a catastrophic short-circuit, resulting in a melted sheath and a major equipment failure. To prevent the coil from touching the sheath, the coil is strung through custom designed ceramic insulating bricks.
Stainless Steel Housing - The housing is the part of the ceramic band heater which holds the ceramic knuckles inside the band together. Several metal alloys are used, for the housing. The most common types of housings are made from stainless steel or stainless steel alloy.
Termination - Since ceramic band heaters are installed in a wide variety of machines, manufacturers must design the heaters to meet certain clearances. The knuckle band heaters might be terminated with terminal box with screw terminals and or leads coming out straight, or in a right angle. Also, manufacturer must be careful that the leads are not exposed to temperatures higher than the maximum rating for the lead wire. In order to prevent lead wire damage from temperature, movement or contamination, the lead wire can be protected with metal conduit or braided metal.
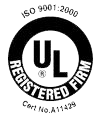
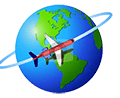
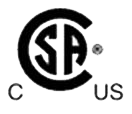
We Ship Our Kapton & Process Heaters To OEM’s & Industry World Wide