Ceramic Band Heaters-Air Cooled, Knuckle Band Heaters-Perforated

Air Cooled Ceramic Band Heaters with Blower, Terminal Box & Closed Shroud
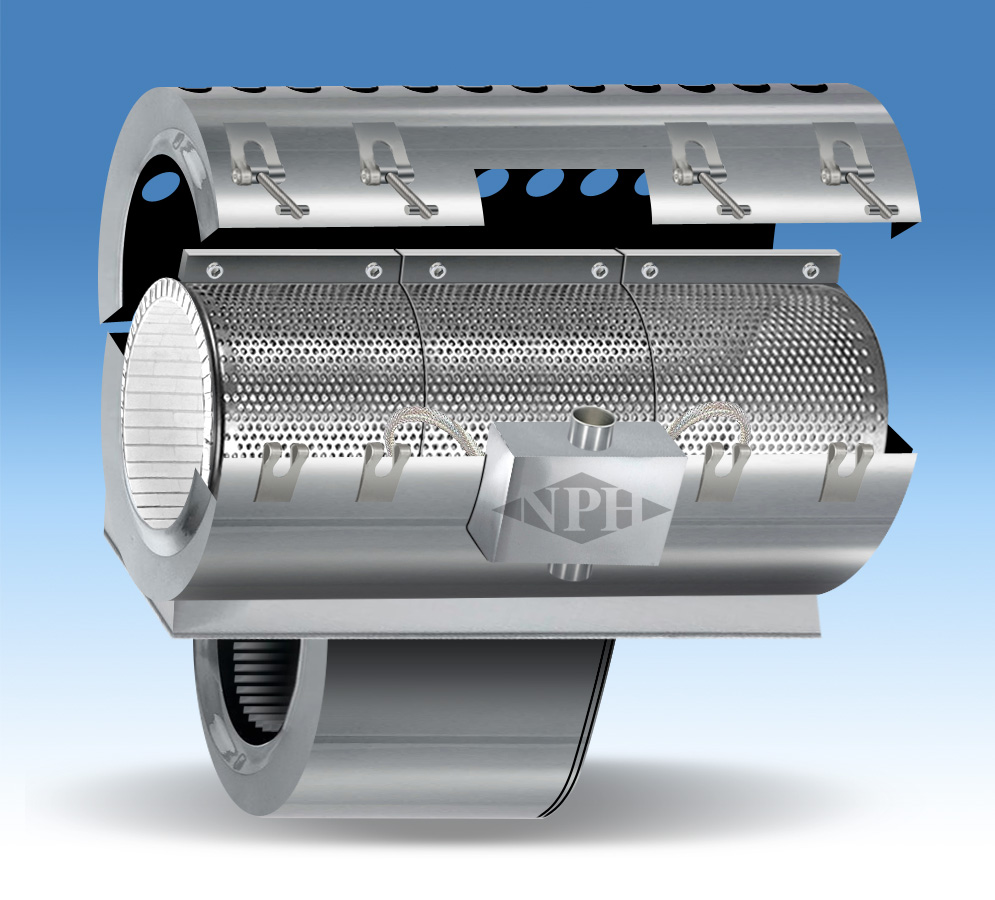
Air Cooled Ceramic Band Heaters with Blower, Terminal box & Open Shroud
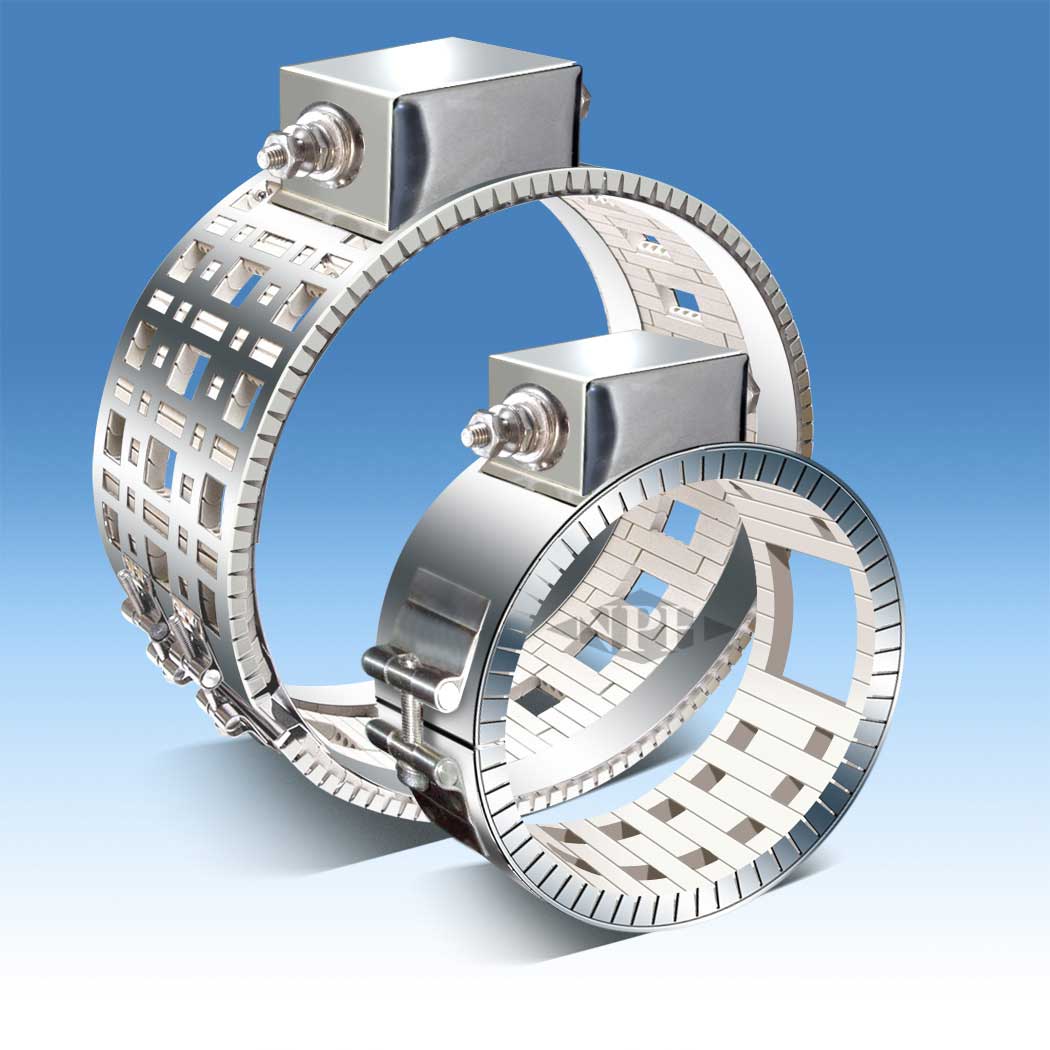
Air Cooled/Perforated Knuckle Band Heaters with Air Cooled/Perfgorated Ceramic Band Heaters with
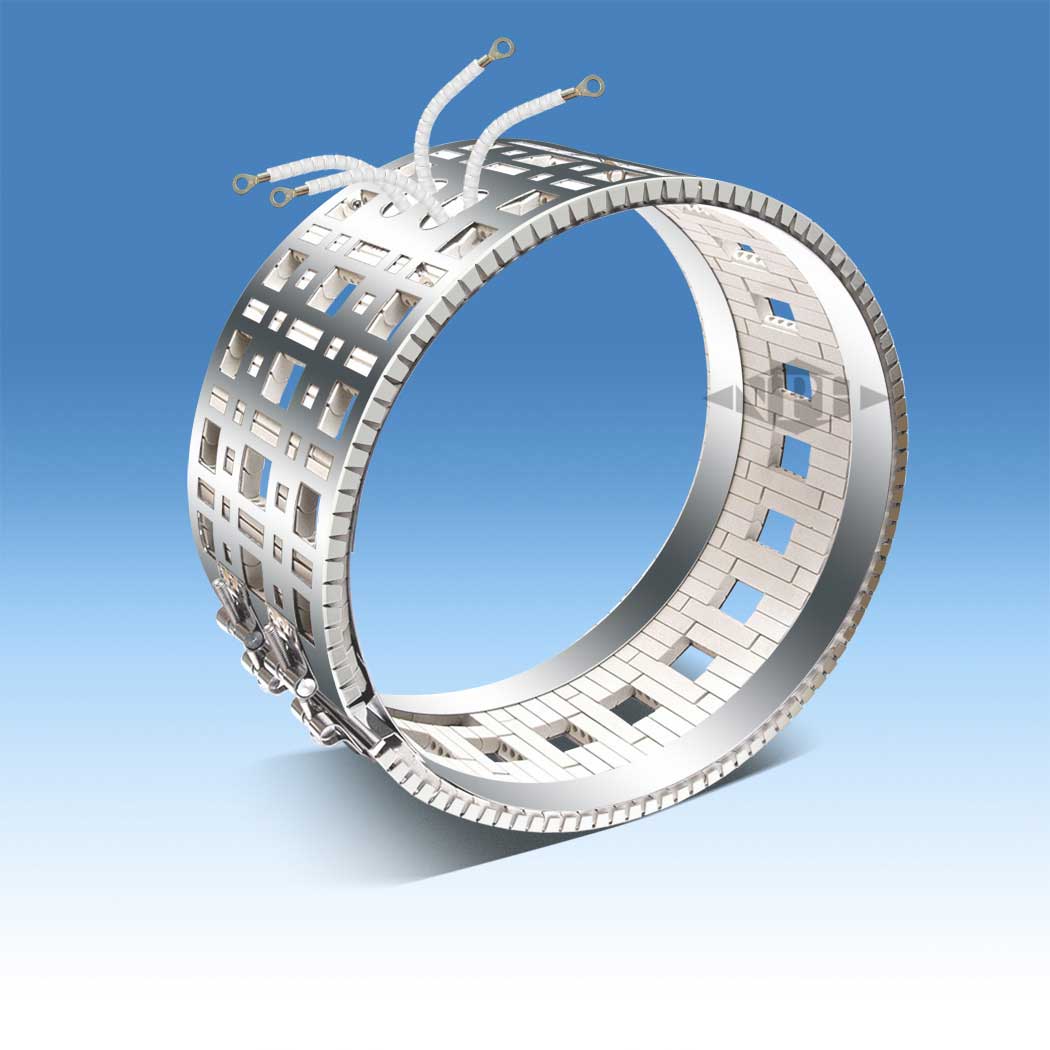
Probe Holes and Terminal Box High Temperature Leads & Ceramic Beads
Design Features for Air Cooled (Blower & Shroud Style) and
Perforated Ceramic Knuckle Band Heaters:
This system was developed to provide another means of heating and cooling high temperature
extrusion processes. Typically cast-in bronze or brass units are used in applications in which
heater temperatures can be in excess of 700°F (371°C). Cast-in bronze or brass
heaters are expensive and since they weigh approximately three times their aluminum counterparts
they are generally considered to be difficult to install.
In response to this challenge, NPH's engineers and partners have developed a low mass,
non-thermally insulated ceramic band heater to work in tandem with a highly efficient stainless
steel sheet metal shroud for high temperature heating and cooling extrusion processes.
Forced air blowers are used for cooling. The ambient airflow enters the shroud, circulates around
the ceramic heater and barrel, removes the heat from the heater and the process and exits the shroud
opposite the entrance port.
Forced air blowers are available in sizes and ratings ranging from 265 CFM to 495 CFM free air.
Construction Characteristics:
The ceramic band is manufactured in two distinct styles:
1. Full coverage type, which has higher watt density capabilities but lesser cooling capabilities
and
2. Rib Cage type, which orients the ceramic insulators and resistance coils in a columnar fashion.
The rib cage design will have less watt density capability than the full coverage type since there
is less area to accommodate resistance coils. Both styles use a perforated outer shell to support
the ceramic insulators and neither style incorporates thermal insulation, which would minimize
cooling efficiency.
The stainless steel shroud is designed with precisely arranged baffles on the inside diameter of
the shroud to break up the laminar airflow from the forced air blower, resulting in an effective
dispersion of the airflow directly onto the heater and the barrel itself. The shroud is a two-piece
clamshell design and also features a heavy duty, rugged flange mount arrangement which can be
customized to accept the blower motor that best suits your extrusion process needs.
Field data has proven it to be very thermally efficient on high temperature applications and
equally effective in standard plastic processing, making the system an excellent choice for machine
retrofits. Consult NPH with your specific application requirements.
Performance Ratings:
Maximum Watt Density: 50 W/in2
Maximum Temperature: 900°F (482°C)
Mechanical:
Standard Width Increments: ½"
Maximum Width: depends on ratio of diameter to Width
Minimum Width: 1-1/2"
Standard Gap: ½", 1/8"
Electrical Ratings:
Resistance tolerance: +10%, -5%
Wattage tolerance: +5%, -10%
Maximum Voltage: 480 single or 3-phase (when applicable)
Maximum Amperage: 25 Amps per circuit
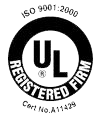
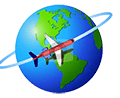
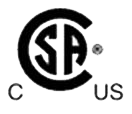
We Ship Our Kapton & Process Heaters To OEM’s & Industry World Wide